Elmsdale Lumber - three phased mill modernization
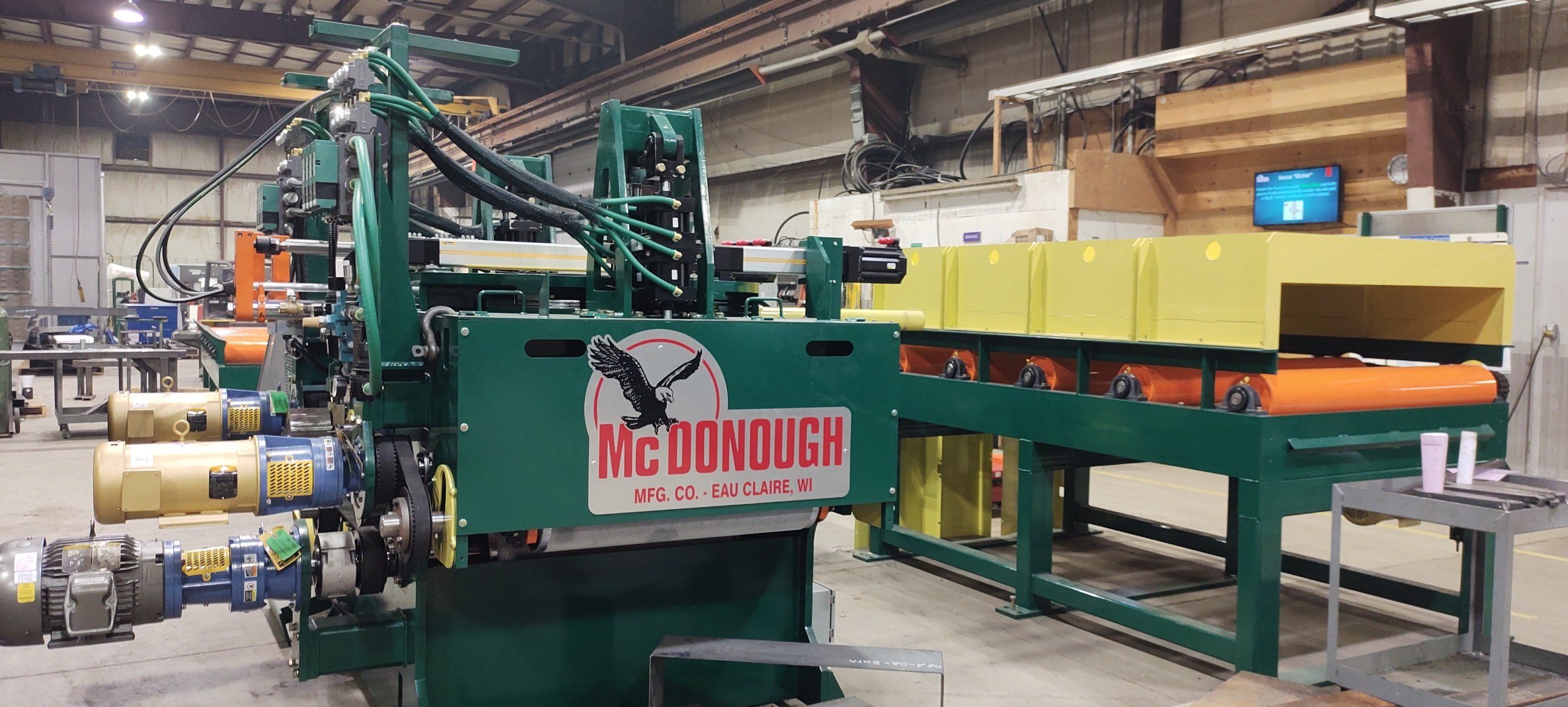
Elmsdale Lumber Company has engaged McDonough Manufacturing for what will be a complete sawmill modernization over the summers of 2022 and 2023. This project will see upgrades to both primary and secondary sawing systems designed to increase both capacity and more importantly yield. The utilization of some of the most modern optimization systems available will ensure that all of the new sawing machinery will yield the highest possible volumes of quality lumber from every piece processed.
Phase One of this project will see the installation of a McDonough Linear Edger System with Reman that will replace the manual edging capacity currently provided as part of the mill's existing combination edger/gang. Fully optimized, this edger will dramatically increase recovery over the manual system while providing the additional ability to handle higher piece counts as well as round-back slabs from the mill's carriage. Handling the round-back pieces will take lines away from the carriage, as the value-added wood fibre from the outside of the slab will be removed by the edger’s reman head, which is inline and immediately upstream of the optimized edger sawbox.
In Phase Two of the project, the gang edger capacity of the original combination system is being replaced with a fully optimized McDonough Curve Sawing Canter-Gang edger. Cants travelling from the mill’s twin scragg saw and carriage will be scanned on their way into a positioning table, which will feed the new single arbor 8” curve sawing sawbox. The McDonough curve sawing system utilizes all electric servo positioning for the sawbox, which is capable of following the calculated curved sawing paths at extremely high accuracy without the heat, power and filtration requirements of less capable hydraulic systems. Cant hold downs and cant positioning is accomplished using the newest in hydraulic servo technology capable of switching between positioning and pressure modes at very high speeds.
Also designed with an inline arbor motor and arbor VFD, the McDonough gang control system will modulate arbor speed as feed speeds vary through different cant widths and thicknesses. As a result, the saw tooth bite and feed speeds can be optimized to maximize throughput and saw performance.
This Canter-Gang system also includes drum chipping canter heads that will surface the outer faces of the cant, removing round slab wood fibre from the system output while providing quality wood chips for sale in local markets. Also positioned by electric servo, the curve canters will follow the optimized curved path in front of the sawbox and size the outer boards before they are cut in the gang saws. The canter heads are fitted with knives that will match the knives in the edger reman unit so that the mill will only need to stock one size knife for the two systems.
Phase Three of this complete mill upgrade will see the replacement of the existing twin circular scragg with a fully optimized McDonough Canter-Quad sawing system featuring log turning, log skewing/offset, solid head conical slant canters and quad guided slab sawing. This system will include fully optimized and automated log rotation, which will feature continuous scanning of the log as it is in the turner to allow for live correction and, therefore, increased turning accuracy. Immediately downstream of the log turner, pieces will be positioned on the fly as they pass between the log turner and the McDonough slant, solid-head canter system.
Log rotation and positioning will be accomplished on the fly using the latest in hydraulic positioning and pressure control technology, which utilizes valves having integrated axis controllers. These valves provide best in class hydraulic control, high response sensitivity high speed communication for integration with associated measuring systems. This system will allow accurate control of logs while being able to depend on the robustness of hydraulics to handle the bumps and knots along log profiles as they are fed into the canters.
Downstream of the canters the logs will pass through the McDonough guided Quad Saw Module which will allow the mill to remove up to four sideboards from each log in accordance with the highest yield solutions provided by the optimizer.
The McDonough Log Turner, Log Positioning Module and Canter-Quad are designed to increase the mill capacity while also dramatically increasing yield over the previously manually operated primary breakdown. Designed to handle logs up to 18” in diameter this system will be the workhorse for the mill, handling the great majority of the logs being processed each day.